CentiMark Blog
Your go-to source for commercial roofing updates!
Welcome to the CentiMark blog, your go-to resource for all things commercial roofing and flooring. Bringing over 55 years of industry experience, we specialize in delivering top-notch solutions for businesses of all sizes. Our team of professionals are committed to delivering superior craftsmanship, exceptional customer service and innovative technologies to meet the unique needs of our clients. Through this blog, we aim to share our expertise and insights on everything from roof repair and maintenance to installation, budgeting, storm damage remediation and beyond! Join us as we explore the latest trends, best practices and industry news that may impact your business’s roofing needs.
Raise the Roof on Summer Prep: Three Steps to Roofing Projects You Can’t Afford to Skip.
As the school year winds down, now is the time to start thinking about summer maintenance and one area that should never be overlooked is your roof. From small private schools to large college campuses, educational institutions tend to quiet down significantly over the summer break. That makes it the perfect window to tackle roof maintenance, repairs or even full replacements without disrupting classes.
Read More >>
Why Summer is Make-or-Break Season for These Three Industries.
Summer is right around the corner and it’s bringing more than sunshine. We’re talking about scorching UV exposure, sudden summer storms and a surge of guests making their way into hospitality and retail facilities across the country. This means that there’s zero room for downtime and a failing roof can hinder your operations during the busiest season of the year. Here’s the top three industries that will be affected and what their roofing priorities should be:
Read More >>
From Roof to Floor – Get Ready for Hurricane, Monsoon and Tornado Season 2025.
As we officially enter the 2025 hurricane season, now is the time to take proactive steps to safeguard your building from potential storm-related damage. From high winds and heavy rain to flooding and flying debris, extreme weather can pose serious risks to your facility, operations and bottom line. Preparing in advance ensures your building is better protected, minimizes downtime and helps you respond quickly should a storm impact your area.
Read More >>
Complete Roofing and Flooring Solutions for Large Construction Projects.
Managing large-scale commercial construction projects presents a number of challenges, particularly when it comes to coordinating multiple vendors for roofing, flooring and painting. The complexity of these projects often leads to misalignments in schedules and quality control. That’s where CentiMark Corporation comes into play.
Read More >>
5 Reasons Why NOW is the Time to Schedule Roof Repairs and Replacements.
If you’ve been waiting for the “right time” to tackle those long-overdue roof repairs or finally take a look into into a full replacement - now is the time. Spring and summer aren’t just warmer months, they’re peak roofing season. Essentially, this season is the perfect window of opportunity to prepare your business for the long winter ahead.
Read More >>
#AskCentiMark Series: Roofing Tips and Trends For Hospitality Facilities.
Resorts, hotels, restaurants and conference centers are evolving and roofing plays a critical role in both guest comfort and the property's overall aesthetic appeal. In this blog, we’ll uncover some roofing tips and innovative tools for the hospitality industry. Our two knowledgeable interviewees for this blog, Emily Zubia, National Account Manager and Jeffrey Patrick, Project Manager are here to help.
Read More >>
#AskCentiMark Series: Steering Automotive Facilities Toward Quality Roofing Solutions.
When it comes to the automotive industry, there’s no “one-size-fits-all” roofing solution. From sleek showrooms to sprawling manufacturing plants, each facility brings its own set of challenges and our roofing pros are here to help.
Read More >>
#AskCentiMarkSeries: How-To Deliver Safe, Durable Roofing for Critical Healthcare Facilities.
Healthcare facilities require a roofing system that not only keeps patients, staff and operations protected but also meets strict codes, cleaning requirements and the needs of sensitive medical equipment. Managing these critical environments can be tough, this blog is your prescription to success!
Read More >>
Beat the Spring Rush: Secure Your Roofing Project Now to Avoid Delays.
Spring is here and the roofing season is about to kick into full gear. Whether you need roof repairs, a full reroof or are in charge of a new construction project and looking at your roofing options, planning ahead is critical to maximizing your budget and meeting deadlines.
Read More >>
Snow is Gone, What's Left Behind?
Now that winter weather is (hopefully!) behind us, it's time to assess any roof damage. With a busy roofing season ahead and summer storms just around the corner, post-winter roof repairs and maintenance are a must. So, what issues should you be looking for?
Read More >>
#AskCentiMark Series: A+ Roofing Tips for Educational Facilities.
IWhether you’re in charge of a small private school or a large college campus, you are deeply familiar with the strict codes and safety regulations that play an integral role in this industry. You need a roof that deserves an A+ and Joshua Attannaiso is here to help! He is well-versed in a wide variety of roofing projects for educational facilities. Let’s dive in:
Read More >>
#AskCentiMark Series: Key Considerations for Roofing in the Warehouse and Manufacturing Industry.
In this blog, we’ll explore key considerations for roofing materials, maintenance strategies and how to manage challenging roofing projects while prioritizing safety for such facilities. Whether you're managing a warehouse or in charge of a large portfolio of manufacturing facilities, this blog has the answers you’re looking for!
Read More >>
Common Mistakes that Lead to Major Roof Damages and Early Replacements.
When you’re in charge of running a business, your daily operations are your main focus. However, one of the most important elements of your building, your roof, is often overlooked. Over time, exposure to various elements can take a toll on your commercial roof. Yet, there are common mistakes that can result in premature roof replacement. Here are the top four overlooked items we’ve noticed over the years.
Read More >>
New Year, New Resolutions: Setting Goals for 2025 to Extend Your Roof’s Life.
The start of a new year is the perfect time to assess your facility’s operational costs and identify areas for improvement. As someone in charge of a commercial facility, optimizing these costs is a daily responsibility. If you want to minimize expenses and ensure safety and compliance to avoid interruptions in your operations, pay special attention to your roof, the largest part of your building envelope. Let’s explore how the condition of your roof may affect your overall operations and develop an action plan together.
Read More >>
Commercial Roofing in 2025: Key Considerations for the Year Ahead.
With the new year underway, significant changes are occurring in the commercial roofing industry. We aim to help you navigate these challenges and provide a smooth commercial roofing experience this year. Let's take a moment to examine what to expect and how to address it.
Read More >>
#AskCentiMark Series: Understanding commercial roof attachment methods.
The attachment method plays a critical role in the longevity, durability and overall performance of your roof system. Whether you’re looking to install a new commercial roof or simply maintain your existing one, having a deeper understanding of the attachment techniques can help you make better roofing decisions.
Read More >>
#AskCentiMark: A Peek Inside Your Roof’s Insulation with Anne Serzz.
Understanding insulation can help you select a material that meets your desired or required R-value which can significantly benefit your building in various ways. Pro tip: Stay proactive in maintaining the best R-value to keep up with any local code changes! The CentiMark team can help you with this by performing a comprehensive roof evaluation and utilizing our thermal imaging drones to locate areas with inadequate insulation or moisture issues.
Read More >>
The Digital Shift in Roof Management: Embracing Technology and Automation.
When managing a commercial property, you have numerous responsibilities, including budgeting, compliance and operations. As you know, optimizing or automating certain tasks can significantly improve your workflow and reduce blind spots. But can these principles be applied to your facility's roof?
Read More >>
#AskCentiMark Series: Why quality roofing matters in food manufacturing facilities.
Buckle up and get ready to learn about mastering the art of roofing food manufacturing facilities! This episode of the #AskCentiMark series gives you some insight into how a properly installed and maintained roof is crucial for you, your business, your employees and the products you manufacture!
Read More >>
#AskCentiMark Series: Best practices to maintain a safe environment up on the roof.
Ready to explore the different elements of maintaining a safe and efficient commercial roof environment? In the latest edition of the #AskCentiMark series, we will review the best practices, training protocols, different ratings and career advice for commercial roof safety on the job site.
Read More >>
#AskCentiMark series: Staying ahead of the game through preventative maintenance with Anne Serzz.
Preventative maintenance helps you find and fix any minor damage to prevent it from becoming a major issue. This type of proactive upkeep can help you with cost savings, significant damage prevention, risk reduction, compliance with your warranty terms and much more!
Read More >>
#AskCentiMark Series: Navigating FM Global requirements for your commercial roofing needs.
If you have FM Global insurance or are considering working with them, understanding their requirements is crucial for your roofing project to safeguard your building. This article will be your guide on all things FM Global by giving you the inside scoop on what it’s like working with them.
Read More >>
#AskCentiMark Series: Roof inspections.
As you may already know, a thorough inspection of your commercial roof that identifies any issues, including those that may not be noticeable to the naked eye, is a crucial first step in keeping your building watertight (or vapor-tight if applicable for your industry). But what does it entail exactly?
Read More >>
2025 budgeting: How to minimize roof-related expenses.
Working on your 2025 budget? Let's look into a few factors that may cause unexpected expenses related to roofing and what you can do as a facility manager or business owner to minimize your risk.
Read More >>
#AskCentiMark Series: The cold truth about roofing in the cold storage industry.
Ready to dive into the roofing challenges and best practices of cold storage facilities? Today’s article gives you some pro tips on ensuring durability, efficiency and cost-efficiency in cold storage roofing.
Read More >>
#AskCentiMark Series: A guide on understanding R-value and energy studies.
In this interview, our very own industry experts explain how energy studies guide the development of tailored roofing solutions for commercial buildings that optimize cost savings, energy efficiency and a healthier workplace environment.
Read More >>
Separating Facts From Fiction: Roof coatings
Looking for a cost-effective way to extend the life of your roof? You've probably heard about roof coatings. There are so many benefits but are there any downfalls? Let's delve into some common concerns and misconceptions surrounding commercial roof coatings that we encounter in the field.
Read More >>
Roof emergency: Now what?
Wow, this summer's weather has not been easy for commercial facilities all over North America. Storms and tornadoes are putting roofs to the test, heat waves are skyrocketing cooling costs and Hurricane Beryl has left devastation in its path. According to forecasters, the remainder of this summer will also be challenging. Let’s make sure you are ready to weather the next storm.
Read More >>
#AskCentiMark Series: Simplifying the complexity of roof management.
It can be challenging to keep a close eye on the condition of your facility's roof. When you are in charge of multiple buildings, things get even more complex. How can you simplify and streamline this process? To find answers, we asked a few commercial roofing industry veterans with decades of experience in both regional and nationwide roofing portfolio management.
Read More >>
Weathering the storm: Making the most of insurance coverage.
This year we may be facing up to 23 named storms and 5 major hurricanes. How can you prepare your commercial buildings for a bumpy ride ahead?
Read More >>
Separating Facts from Fiction Series: Addressing metal roof concerns.
Metal roofs, while very popular with commercial facilities, are not immune to myths and misconceptions like any other roofing or siding material. Let's look into some of the common concerns we hear in the field and address them!
Read More >>
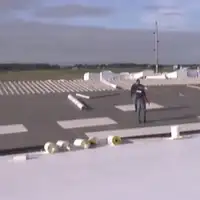
The Role of Insulation in Your Roof Assembly
Whether you are in hospitality, manufacturing, cold storage or any other industry, excessive moisture in your building can result in a number of issues ranging from mold to water damage and poor air quality. Did you know the state of your roof's insulation may play a significant role in all of this?
Read More >>
Roofing Details Make a Difference: An Up Close Look at Your Roof's Components
Paying close attention to roof components like drains, scuppers, flashings, pipes, pitch pans and more is vital for proper maintenance and ensuring that your roof will withstand the elements. Let's look closer at those items to understand their function and how to address their condition during your seasonal maintenance.
Read More >>
Weathering the Elements: Region-Specific Commercial Roofing Challenges in North America
North America has a wide range of climates and weather patterns, including cold and stormy winters in the North and scorching heat in the South. It also has a wide variety of landscapes, from rainforests to deserts. This diversity poses unique challenges for commercial facilities when it comes to roofing. Let's explore the region-specific commercial roofing challenges in North America and discuss how you can address these issues to ensure the longevity and performance of your roof.
Read More >>
Separating Facts from Fiction Series: TPO Roofing Concerns Addressed
In recent years, Thermoplastic Olefin (TPO) roofing has gained enormous popularity due to its energy efficiency, long-lasting performance and resistance to fungi and UV rays. However, like any widely used material, TPO roofing is not immune to misconceptions and myths, mainly because the technology is relatively new compared to some other roof systems. This article will address common TPO roofing myths and concerns and clarify misunderstandings.Read More >>
Commercial Roofing: Effective Strategies to Prevent Premature Replacement
As the price of labor and materials continue to rise, it is important to focus on long-term strategies regarding roof systems in order to maximize your budget. Here are some of the top strategies to protect your facility's roof:Read More >>
How to Choose the Right Roof System for Your Commercial Facility
Selecting the optimal roof for your commercial facility is an important decision that can greatly influence the operating expenses of your building. Given the multitude of options, each tailored to specific requirements, it is imperative to thoroughly assess your facility's precise needs before reaching a decision.Read More >>
A Glimpse into Innovative Technologies
Commercial roofing embraces innovation with drone inspections, infrared scans, green roofing, CentiVision and online portals. Transforming traditions for efficient, cost-effective and sustainable solutions, prioritizing safety and customer education.Read More >>
CentiMark's CentiVision: A Visual Approach to Roofing
The commercial roofing industry is no exception in an ever-evolving world of technology and innovation. With over two years of successful implementation, CentiVision remains a trusted solution for businesses across North America, eliminating uncertainty in their roofing projects.Read More >>
Five Keys to Finding a Reputable Commercial Roofing Contractor
Your facility's roof is the first line of defense against the harsh elements of nature. Its role in protecting your business assets and your associates is of vital importance. Therefore, when partnering with a commercial roofing contractor, here are five key considerations that should be taken into account to ensure an informed decision is made and your investment dollars are prudently spent.Read More >>
Roof Budget Blues: Navigate Uncertainty With Confidence
Reroof or repair has always been a question of precise timing. However, in the current economic climate, many businesses have difficulty making capital improvement decisions such as roofing projects in order to preserve the budgets. Therefore, in some cases roofing projects may not be feasible at the moment. So what can you do when you have to delay your reroof due to budgetary concerns?Read More >>
Summer Roof Checkup: 10 Frequently Overlooked Items That Deserve Your Attention
Given that your facility's roof serves as the primary protection for your business operations, it may require repairs or maintenance to ensure it's performing at its best and is 100% watertight. Numerous defects with commercial roofs often remain undetected for an extended period of time, escalating into significant damage. Let's explore these frequently overlooked items that may be lurking just above you.Read More >>
Help Your Roof Beat the Heat: Optimizing Temperature Resistance
This summer unleashed scorching temperatures across North America. On July 3rd, we witnessed the record-breaking hottest day ever documented on Earth. As the sweltering heat takes its toll, your commercial facility's cooling expenses may spiral out of control. So, how can you better adapt to these blistering conditions? The solution might be your facility's roof.Read More >>
Qualifying Your Roofing Project: What is the Optimal Solution for Your Facility
Your commercial roof serves as your primary shield against the elements, safeguarding everything beneath it, including your staff, machinery, stock, real estate and more. Furthermore, it exerts a significant influence on your building's energy efficiency and potential resale worth. With so much on the line, ensuring you make correct, educated decisions regarding your roof condition is crucial.Read More >>